In the EU in 2021, 5% of annual emissions were produced by the steel industry. As the EU aims for carbon neutrality in industry by 2050, significant and rapid changes must be made. The traditional steel production method, which is currently used for 65% of the steel production in the EU, produces approximately 1.8 tonne of CO2 per tonne of steel. These emissions come as coking coal is used for many parts of the process, mainly the provision of high-grade heat (>1400°C), and production of reducing gases to convert the iron ore into the steel product.
Hydrogen-based Direct Reduction of Iron (H-DRI) is one of few deep decarbonisation options available for the steel sector, while offering the potential to avoid the other environmental impacts of fossil fuel combustion that CCS cannot offer e.g. harmful air pollution. This has led to the H-DRI decarbonisation option being chosen by many of the world’s leading steel producers. Tata Steel IJmuiden is an example of this, as in 2021 they announced the intention to transition to H-DRI, with the intermediate step of natural gas DRI. For my energy science Masters’ thesis, I analysed the case study of Tata Steel IJmuiden, and the cost and energy efficiency of competing supply chains for the H-DRI process.
H-DRI steel production involves the use of hydrogen gas, as opposed to traditional coking coal or natural gas. This occurs in a direct iron reduction (DRI) shaft furnace, where the hydrogen is injected both as the heat source and as the reducing gas, removing the oxygen from the iron ore during the steel making process. DRI shaft furnaces are commercial technologies since the 1970’s and are commonly used for steel making in areas with cheap natural gas today. The reduced iron product of the DRI shaft furnace can be used to make semi-finished crude steel if used as an input in an Electric Arc Furnace (EAF), or it can be made into an intermediate form for storage called Hot Briquetted Iron (HBI). Both products allow for the spatial separation of the steel production process.
Traditionally, steel production is an energy intensive process, and this isn’t expected to change. It is estimated that for the production of 1 tonne of steel between 50-70 kg of hydrogen will be required for the H-DRI process, with approximately 700 kWh of electricity required for the electric arc furnace. For green hydrogen production water electrolysis from dedicated renewable energy is required as per EU taxonomy. As such the renewable energy required for green steel is significant, especially for steel plants looking to retain a large capacity. To continue production of 7 Mt a year with 100% green hydrogen, Tata Steel IJmuiden would require approximately 380 kton of hydrogen. This hydrogen production, and the use of renewable electricity for the electric arc furnace, will equate to approximately 6-9 GW of offshore wind in the North Sea being required for green steel operations by Tata Steel IJmuiden.
Abundant, low-cost renewable energy resources are to some extent lacking around the majority of the largest EU steel plants in the north west and centre of Europe, with the potential exception of this offshore wind in the North Sea. Tata Steel IJmuiden is ideally located to take advantage of this, but with indications of low-cost hydrogen production elsewhere with the potential to export, and the location of new H-DRI operations in areas with very low cost solar (e.g. H2steel, Arcelor Mittal in Spain) there is a need to consider the different H-DRI supply chain options.
The supply chains considered in my thesis for the H-DRI process in 2030, 2040, and 2050 were as follows:
· Continued production of steel in IJmuiden using locally produced hydrogen
· Continued production of steel in IJmuiden using hydrogen imported from outside the Netherlands
· Relocation of the DRI shaft used for iron production away from IJmuiden to a location abroad combined with hydrogen production. The steel making remains in IJmuiden with the import of the intermediate product hot briquetted iron (HBI) for use in the EAF.
· Relocation of the full steel making process (DRI shaft & EAF) with hydrogen production and the import of the semi-finished crude steel for finishing and distribution
Each of these possible supply chain options are pictured in the figure below, with the locations considered for relocation being the Pilbara region in Australia, northern Sweden, and northern Spain.
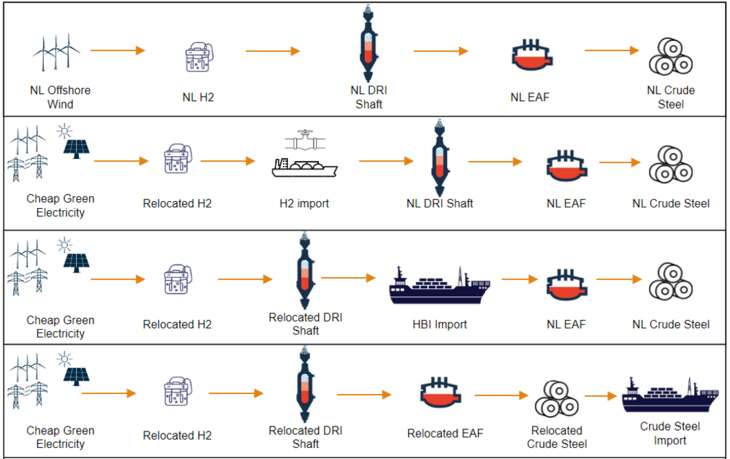
Figure 1. The supply chains considered for the Hydrogen-based Direct Reduced Iron steel making process. They were considered for the years 2030, 2040, and 2050, with the locations for relocation being Australia, Sweden, and Spain. HBI - Hot Briquetted Iron , DRI shaft – Direct Reduced Iron shaft for ironmaking, EAF - Electric Arc Furnace
My comparison of these supply chains indicates that the cost of production of H-DRI steel is strongly dependent on the electricity price and electrolyser capacity factor, and the subsequent cost of hydrogen. The economic and energetic costs of hydrogen imports are a barrier to the import of hydrogen, with the costs of hydrogen production from North Sea offshore wind calculated to remain competitive with the costs of hydrogen production in the considered alternative regions. This means that Tata Steel’s location in IJmuiden, can be relatively cost competitive as a result of this close proximity to offshore wind in the North Sea, while having such a short supply chain for hydrogen production with fully local steel production is the most energy efficient supply chain.
If hydrogen imports were to be considered the pipeline appears the most cost effective, especially when the costs expected for the European Hydrogen Backbone1 were considered (2040 onwards). This could be significant for other European steel producers without access to sufficient renewable resources who will require hydrogen imports or relocation.
The import of hydrogen by ship in all forms considered (ammonia, liquid hydrogen, and the liquid organic hydrogen carrier DBT) is calculated to be uncompetitive with all the other supply chains considered, with high costs for the infrastructure and conversion/reconversion units, and energy inefficiencies responsible for this. If considering the import of steel products hot briquetted iron (HBI) import is not logical, as the reason for relocation of the DRI shaft would be to capitalize on low-cost, abundant renewables, which is also the perfect place to locate an EAF, which consumes approximately 700kWh per tonne steel. This and the energy penalty of reheating cold HBI in the EAF means the import of semi-finished crude steel appears to be the better option.
On a cost and energy efficiency basis, it appears that future H-DRI supply chains will dominantly be; maintained operations where low-cost hydrogen production exists, hydrogen import via pipeline over short distances for steel production (especially following expansion of the European Hydrogen Backbone), or the import of semi-finished crude steel to the current for finishing at current location of operations.
For Tata Steel IJmuiden the abundant and relatively low-cost offshore wind from the North Sea, coupled with the bad economics of hydrogen imports, leads to a very strong business case for the continuation of operations with H-DRI in IJmuiden. This will, however, require a large share of the offshore wind energy from the Dutch North Sea, approximately 6-9 GW. The recent decision of the German government with the European Commission to use state aid to award a €1bn subsidy for a H-DRI shaft furnace and electrolyser to steel giant Salzgitter will likely further complicate any decisions over H-DRI supply chains however, with job security for citizens and security of supply of materials also factors of increasing importance for European countries and the EU as a whole.
1 European Hydrogen Backbone. 2020 https://ehb.eu/files/downloads/2020_European-Hydrogen-Backbone_Report.pdf
Shape common futures together with us
Get in contact